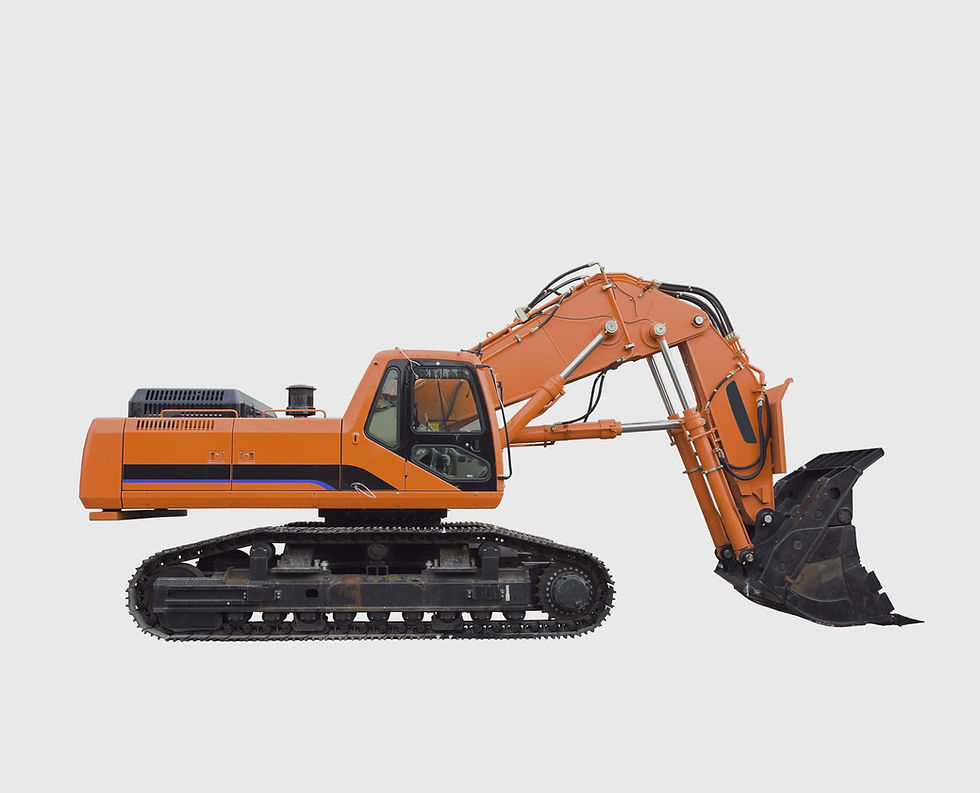
When it comes to excavators, operators and fleet managers often focus on high-profile components like engines and hydraulics. However, the alternator is a crucial yet often overlooked component essential for powering the excavator's electrical systems and ensuring consistent operation on demanding job sites. In this comprehensive guide, we explore the vital role, importance, maintenance, troubleshooting, and replacement considerations of the alternator in excavator engines.
Understanding the Excavator Alternator
An alternator is fundamentally a generator that transforms mechanical energy from the excavator's engine into electrical energy. Its primary tasks include recharging the battery and powering various electrical components, from lights and sensors to computer systems and hydraulic controls.
Key Functions of the Excavator Alternator
1. Battery Charging
A key responsibility of the alternator is maintaining a fully charged battery. During engine operation, the alternator replenishes the battery, compensating for energy consumed during start-up and continuously supporting the electrical load. This reliability ensures smooth operations and timely startups.
2. Powering Electrical Systems
Modern excavators rely heavily on sophisticated electrical components for precise, controlled operation. The alternator delivers a consistent and stable electrical current, ensuring uninterrupted function of vital systems including dashboards, telematics, GPS navigation, climate control, and diagnostic modules.
3. Supporting Hydraulic Controls
Although hydraulic systems are mechanically driven, they incorporate crucial electrical components such as solenoid valves, controllers, and sensors. The alternator guarantees a consistent electrical supply, enabling accurate and efficient hydraulic operation essential for performance and safety.
4. Enhancing Machine Efficiency
The alternator indirectly boosts the efficiency and performance of an excavator by ensuring electrical systems are always optimally powered, thus minimizing disruptions and enabling seamless operations even under heavy load conditions.
Detailed Components and Operation
The primary components of an alternator include:
Rotor: The rotating magnet producing a magnetic field, driven directly by the engine.
Stator: Stationary copper windings where electrical current is induced.
Rectifier: Converts generated alternating current (AC) into direct current (DC) suitable for the excavator’s systems.
Voltage Regulator: Stabilizes voltage output to prevent electrical surges and damage to sensitive components.
Major Manufacturers of Excavator Alternators
Several industry leaders produce robust, high-performance alternators tailored specifically for excavators:
Bosch: Trusted globally, Bosch alternators are frequently installed in Caterpillar, Komatsu, and Volvo excavators.
Denso: Preferred for Japanese-built machinery, found prominently in Hitachi, Kobelco, Hyundai, and Takeuchi excavators.
Delco Remy: Widely used in Case, JCB, New Holland, and Bobcat excavators.
Mitsubishi Electric: Common in Komatsu, Sumitomo, Kubota, and other popular Japanese excavator brands.
Prestolite Electric: Known for reliable performance in various heavy machinery including excavators by Terex and Liebherr.
Identifying Common Alternator Issues
Alternators are durable but not immune to wear. Typical issues include:
Bearing Failure: Manifested by noise or decreased efficiency.
Worn Brushes: Causes intermittent or diminished electrical output.
Faulty Rectifiers: Results in insufficient battery charging or fluctuating electrical supply.
Signs of alternator trouble include:
Flickering or dim lights
Dashboard warning indicators
Battery drain or frequent replacements
Erratic electrical or hydraulic system performance
Audible noises such as grinding or whining from the alternator
Essential Maintenance Tips
Proper maintenance significantly enhances alternator life and reliability. Recommended practices include:
Regularly inspecting belt tension and integrity
Periodically checking and monitoring voltage output
Keeping the alternator free from debris, dust, and mud
Promptly addressing minor issues before they escalate
When to Replace an Excavator Alternator
Timely replacement of a faulty alternator can prevent costly downtime and prolonged operational disruption. Opting for quality refurbished OEM alternators can save money while maintaining optimal performance.
Why Choose Vikfin for Your Alternator Needs?
Vikfin specializes in providing high-quality, thoroughly tested used OEM alternators at a fraction of the price of new parts. Our extensive inventory covers major manufacturers, ensuring compatibility and reliable performance for your excavator. Trust Vikfin to reduce your downtime, lower maintenance costs, and enhance operational efficiency.
Final Thoughts
The alternator, though sometimes overlooked, is an indispensable component of excavator performance and reliability. Regular attention to maintenance, timely diagnosis, and choosing a trusted provider like Vikfin for replacements ensures continuous productivity and peace of mind.
#ExcavatorParts #Alternator #HeavyMachinery #ConstructionEquipment #OEMAlternators #Vikfin #ExcavatorMaintenance #MachineryTips #ExcavatorRepair #BoschAlternators #DensoAlternators #DelcoRemy #MitsubishiElectric #Prestolite #HeavyDutyParts #ReliableExcavators #EquipmentEfficiency #ExcavatorExperts #UsedOEMParts #ConstructionLife
Comments