The True Cost of Downtime: How Vikfin’s Used Parts Keep Your Excavators Running
- RALPH COPE
- Feb 27
- 5 min read
Updated: Feb 28
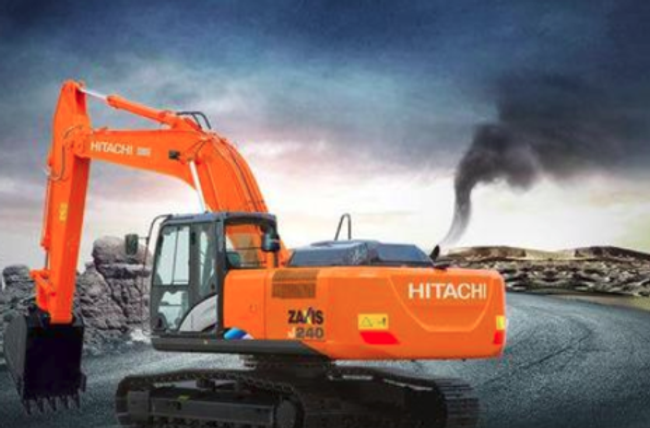
Time is money. In industries like construction, mining, and bulk material handling, a single day of unexpected downtime can mean hundreds of thousands—if not millions—of rands in lost revenue. When an excavator breaks down, operations come to a screeching halt, delaying project timelines, increasing labor costs, and frustrating clients.
Yet, many fleet owners and operators overlook one of the most cost-effective solutions to minimizing downtime: fast, reliable, high-quality used OEM parts.
Vikfin specializes in providing tested and trusted used OEM excavator parts at a fraction of the price of new ones—without the long lead times of ordering new parts. Our mission is simple: Get your excavator back to work as quickly as possible while saving you money.
In this blog, we’ll break down:
The real financial cost of machine downtime.
Why waiting for new parts is a losing game.
How Vikfin’s massive inventory of used OEM parts is a game-changer.
A real-world case study proving how fast part replacement saved a client from disaster.
The Real Cost of Excavator Downtime
If your excavator goes down, you’re not just looking at repair costs—you’re facing a ripple effect of financial losses. Here’s how downtime hits your bottom line:
1. Lost Revenue from Delayed Operations
Excavators are critical in industries that rely on heavy earthmoving machinery. When a machine is idle, everything connected to it stops:
In construction, delays push back entire project timelines, leading to penalty fees in contracts.
In mining, a halted excavator means fewer tons of material moved per day, lowering revenue targets.
In scrapyards, delays result in a backlog of metal that isn’t being processed, impacting cash flow.
A 20-ton excavator in construction typically moves 300–500 cubic meters of material per day. If downtime lasts a week, that’s thousands of cubic meters of lost productivity, which translates to hundreds of thousands in lost revenue.
2. Increased Labor Costs
Downtime doesn’t just affect machines—it affects workers, too. Idle operators and site workers still need to be paid, even though their productivity is zero. If your project involves subcontractors, delays can mean paying for extra days of work, pushing labor costs through the roof.
3. Equipment Rental Fees
Many contractors rent backup machines when their primary excavators are down. Depending on the size and type of excavator, rental rates can range from R20,000 to R100,000 per week. This adds an unnecessary financial burden—especially when a fast part replacement would have solved the issue.
4. Contract Penalties and Reputation Damage
Construction and mining contracts often include strict deadlines, with penalty clauses for delays. Missing project milestones can result in massive financial penalties—or worse, lost future business opportunities.
For plant hire businesses, an unreliable fleet can damage client trust and lead to lost contracts. If customers believe your machines are prone to breakdowns, they’ll simply go to a competitor.
5. Cost of Buying New Parts vs. Used OEM Parts
When an excavator part fails, many operators immediately think of ordering a brand-new replacement from the OEM. Here’s why that can be a terrible financial decision:
New OEM parts often have long lead times—sometimes weeks or months for delivery.
The cost of a new part is often 2–5 times higher than a high-quality used OEM part.
The longer you wait for new parts, the higher your downtime costs climb.
Example:A new slew motor for a 20-ton excavator can cost R180,000+ and take 4–6 weeks to arrive.A high-quality used OEM slew motor from Vikfin can be 50–70% cheaper and available immediately.
How Vikfin Eliminates Downtime with High-Quality Used Parts
At Vikfin, we understand that every hour of downtime costs money. That’s why we stock a massive inventory of used OEM excavator parts, ready for immediate dispatch.
1. Huge Stock of Critical Components
We specialize in parts that commonly fail on excavators, including:
✅ Engines – Complete units, fully tested.✅ Hydraulic cylinders – Boom, bucket, dipper arm.✅ Slew motors – Essential for cab rotation.✅ Final drives – Keeps tracks moving.✅ Cabs – Used but structurally sound.✅ Undercarriage components – Steel tracks, rollers, sprockets.✅ Valve banks & pumps – Key hydraulic components.
All our parts come from tested excavators, ensuring they function just like new but without the excessive cost.
2. Fast, Reliable Delivery
We know that speed matters. Our logistics team ships parts quickly, often within 24 hours of your order. Whether you need a slew motor in Cape Town or a hydraulic cylinder in Durban, we make sure you get it fast.
3. Cost Savings Without Quality Compromise
Why pay for brand-new parts when a tested OEM part does the same job for half the price? Vikfin helps clients maximize profitability by:
💰 Offering huge cost savings (50%+ off new OEM parts).⚙️ Providing only high-quality tested parts.🚀 Minimizing downtime by getting parts to you fast.
Case Study: How Vikfin Saved a Mining Contractor from a Costly Disaster
The Problem
A major mining contractor in South Africa experienced a catastrophic slew motor failure on a Komatsu PC300 excavator. The breakdown happened in the middle of an urgent contract to move 500,000 tons of material.
With a tight deadline, the client faced:
❌ R475,000 per day in lost revenue.❌ Costly penalties for contract delays.❌ A 6-week wait time for a brand-new OEM slew motor.
The Solution
The contractor called Vikfin in a panic. Within an hour, our team confirmed we had a high-quality used OEM Komatsu PC300 slew motor in stock.
✅ The part was shipped the same day.✅ Installation was completed within 48 hours.✅ Total cost: 60% less than a new OEM part.
The Result
By sourcing a fast and affordable used OEM part from Vikfin, the contractor:
✔️ Saved over R1.2 million in lost revenue.✔️ Avoided penalties for project delays.✔️ Kept their mining operations running smoothly.
Conclusion: Don’t Let Downtime Drain Your Profits
Every excavator owner knows that breakdowns are inevitable, but prolonged downtime isn’t. The key to maintaining a profitable and efficient operation is quickly sourcing high-quality replacement parts at the right price.
Vikfin helps businesses cut costs, reduce downtime, and maximize profitability by offering:
✅ A massive inventory of used OEM parts✅ Lightning-fast delivery across South Africa✅ Proven quality and reliability✅ Unbeatable prices compared to new OEM parts
When your excavator goes down, every hour counts. Don’t waste time waiting for expensive new parts. Call Vikfin and get back to work—fast.
📞 Contact us today for a quote on high-quality used OEM excavator parts!
#ExcavatorParts 🚜#UsedOEMParts 🔩#ExcavatorRepairs 🏗️#MinimizeDowntime ⏳#ConstructionIndustry 🏗️#MiningEquipment ⛏️#EarthmovingMachinery 🌍#HeavyMachinery 🔧#ExcavatorMaintenance 🛠️#SaveOnRepairs 💰#VikfinParts ✅#QualityUsedParts ⚙️#OEMExcavatorParts 🔄#FastPartReplacement 🚀#ExcavatorHydraulics 💦#FinalDrives 💪#SlewMotors 🏗️#ReduceProjectDelays ⏱️#MaximizeProductivity 📈#ExcavatorEfficiency 🔝
Comentarios