The True Cost of Downtime—And How Used OEM Parts Save the Day (A Tale of Lost Profits, Broken Machines, and the Parts Supplier That Saves the Day)
- RALPH COPE
- 2 days ago
- 4 min read
Updated: 1 day ago
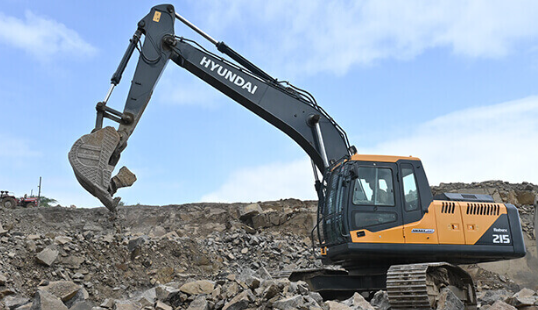
In every epic story, there’s a villain. In construction and earthmoving, that villain doesn’t wear a cape or twirl a mustache—it wears grease, rust, and a blank look on your operator’s face.
We’re talking about downtime.Every contractor’s nightmare.Every plant hire operator’s biggest threat.And it’s far more expensive than most people realize.
But every villain needs a hero. And that’s where Vikfin comes in—with tested, affordable, ready-to-install used OEM parts that get your machine moving again before downtime eats another cent of your profit.
This blog breaks down the real cost of downtime, the hidden dangers of waiting for new or aftermarket parts, and how smart businesses across South Africa are turning to Vikfin to save the day—again and again.
The High Price of Downtime (That Nobody Talks About)
Most operators think of downtime in terms of parts cost.The cylinder failed? R60,000.Final drive died? R120,000.Not cheap—but manageable.
But that’s just the beginning. The real danger is what downtime costs you every hour your machine isn’t working.
Let’s break it down:
🚧 For a Contractor:
Delayed site work = penalties from the client
Standing crew = wasted labour hours
Rented backup equipment = added expenses
Missed deadlines = lost trust
🚜 For a Plant Hire Operator:
Idle machine = zero income per day
Cancelled bookings = angry clients who go elsewhere
Reputation damage = future revenue lost
And it adds up—fast.
Real-World Example: Downtime Disaster in Gauteng
A contractor had a Volvo EC210B with a failing slew motor. They ordered a new OEM motor through the dealer—quoted at R140,000 with a 3-week lead time.
By the end of Week 1:
The crew was idle
A backup machine had to be hired
The project deadline slipped
The penalty clause kicked in
Total cost of delay:
Labour: R28,000
Machine rental: R55,000
Penalty fees: R35,000
Stress, frustration, and lost client trust: priceless
All because of one part.
Enter Vikfin: The Downtime Killer
The contractor called Vikfin in desperation. Within 24 hours, we supplied a tested, used OEM Volvo slew motor for R65,000.
Same-day delivery
Bolted straight on
Machine back on-site the next day
Total savings: over R90,000
That’s what we do at Vikfin. We turn downtime into uptime—without breaking your bank.
How Used OEM Parts Save You From Downtime Disaster
Here’s why used OEM parts are the fastest, safest, most cost-effective solution when downtime strikes:
✅ 1. Immediate Availability
No 3-week lead times. No customs delays.We’ve got the parts—in stock and ready to ship.
From:
Engines
Final drives
Boom cylinders
Slew motors
Valve banks
Track adjusters
Cabs
To entire undercarriages
We specialize in 20- and 30-ton excavators—and our yard is always full of tested, OEM-quality components.
✅ 2. Exact Fitment, First Time
Knockoff parts or aftermarket imports often need grinding, welding, or adapting—costing you more time.
Used OEM parts from Vikfin are:
The correct fit
The right spec
From the same brand and model
Designed to drop in and work
No stress. No modification. Just performance.
✅ 3. Tested, Trusted, Guaranteed
Every part that leaves Vikfin has been:
Inspected for wear
Cleaned and reconditioned
Pressure tested or compression tested
Verified against OEM specs
We don’t just hope it works. We prove it does.
✅ 4. Dramatic Cost Savings
Used OEM parts cost 30–70% less than new parts—and still last thousands of hours if properly installed.
You save money today, and because you’re avoiding low-quality knockoffs, you also save tomorrow.
What Downtime Really Costs You Per Hour
Let’s do the math for a 20-ton excavator in the plant hire game:
Downtime Factor | Estimate per Day |
Lost rental income | R8,000 – R12,000 |
Operator standby | R1,200 |
Penalties from clients | R3,000 – R5,000 |
Admin & rescheduling costs | R1,000 |
Average daily loss: R15,000 – R20,000Over 5 days = R75,000 – R100,000Over 2 weeks = Up to R250,000
Now compare that to:
A new final drive at R150,000 (3 weeks wait)
A used OEM final drive from Vikfin at R65,000 (next-day delivery)
The math is obvious. The choice is clear.
Downtime Horror Story: Limpopo Plant Hire Business
One of our clients in Limpopo had a Komatsu PC200 down with a faulty valve bank. They waited 10 days for a new part—R96,000.
Before the part arrived, the operator “tested” the machine, ruptured a hydraulic line, and damaged a second cylinder.
Total repair cost?
R96,000 for the valve bank
R33,000 for the damaged cylinder
R24,000 for cleanup and fluid replacement
14 days lost hire = R112,000
That’s R265,000 gone.
They now buy all parts through Vikfin. We delivered a used OEM valve bank the next day—for R40,000.
Why Contractors Trust Vikfin
Here’s what makes us South Africa’s go-to supplier of used OEM excavator parts:
🔧 We Specialize
We only deal in excavators—and we know every inch of them. From Komatsu and Volvo to Doosan, Hitachi, Sumitomo, and Caterpillar—we strip, test, and supply with precision.
🛠️ We Test Everything
We won’t sell it unless we’d fit it ourselves. We pressure-test cylinders, run engines, and inspect gear teeth with micrometers.
💰 We Beat Any Legitimate Quote
We guarantee the best price in the market for comparable OEM used parts. Why? Because we want your trust—and your repeat business.
🚛 We Deliver Nationwide
No matter where your machine’s broken—Gauteng, Mpumalanga, Limpopo, Free State—we’ll get the part to you fast.
What Our Clients Say
“Vikfin saved us R80k and got our Doosan back up in two days. Aftermarket part didn’t fit—wasted a week. Never again.”– Bheki M., Plant Hire Owner, KZN
“Final drive blew at the worst time. OEM quoted 3 weeks. Vikfin had it ready the next morning.”– Dan R., Earthmoving Contractor, Gauteng
“Their used parts feel like new. Haven’t had a single return.”– Nico T., Excavator Mechanic, North West Province
Final Thoughts: Downtime Is the Enemy. Vikfin Is the Answer.
You can’t control every breakdown. But you can control how long it takes to bounce back.
And in construction, speed is survival.Every hour matters. Every rand counts.You need a supplier who acts fast, tests thoroughly, and delivers consistently. That’s what we do—day in, day out.
So next time your excavator’s down, don’t waste time calling overseas or fighting with fake parts.Call Vikfin. We’ll save your day—and your budget.
Machine Down? Let’s Get You Back on Site—Fast.
✅ Call or WhatsApp Vikfin✅ Get a quote in minutes✅ Receive a tested OEM part✅ Save time. Save money. Kill downtime.
📞 Vikfin – Because Every Hour Counts
#Vikfin#UsedOEMParts#ExcavatorDowntime#ConstructionDelays#SaveTimeSaveMoney#FinalDriveFix#BoomCylinderRepair#HydraulicSystemFailure#SlewMotorSolutions#ExcavatorBreakdown#MachineUptime#ExcavatorPartsSouthAfrica#TestedParts#RefurbishedHydraulics#NoMoreDelays#DowntimeIsTheEnemy#PlantHireProblems#JobsiteSolutions#ExcavatorRepairs#VikfinToTheRescue
Comments