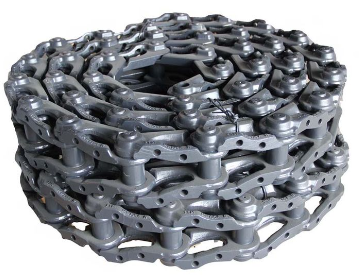
In the world of earthmoving machines, every component plays a crucial role in ensuring optimal performance and longevity. Among these components, the master link in steel excavator tracks stands out as a key player. In this blog post, we'll delve into the importance of the master link, how to locate it within the tracks, and the proper steps to remove it for essential maintenance tasks.
Understanding the Master Link:
The master link in steel excavator tracks serves as a pivotal connection point, allowing the tracks to be separated when necessary. This separation is vital for efficient replacement of critical components such as final drives, idler wheels, and track adjusters. By having a designated link that facilitates disassembly, operators can carry out maintenance and repairs with greater ease and precision.
Locating the Master Link:
Identifying the master link within the complex structure of steel excavator tracks requires a keen understanding of the machine's design. Typically, the master link is strategically positioned in a specific section of the track assembly. Manufacturers often provide clear indications in the user manual or equipment documentation to guide operators to the location of the master link.
To locate the master link:
Refer to the machine's user manual or technical documentation.
Inspect the track assembly for markings or unique features indicating the presence of the master link.
Identify any section where the tracks can be easily separated, signaling the master link's position.
Importance of Proper Maintenance:
Now that we understand the role and location of the master link, it's crucial to emphasize the importance of regular maintenance. Proper maintenance not only ensures the longevity of the master link but also contributes to the overall efficiency and reliability of the excavator.
Maintenance steps:
Regularly inspect the master link for signs of wear, corrosion, or damage.
Keep the master link adequately lubricated to prevent friction and reduce wear.
Follow the manufacturer's guidelines for scheduled maintenance and replacement intervals.
Knocking Out the Master Link for Maintenance:
When it comes to replacing components or performing maintenance that requires separating the tracks, knowing how to knock out the master link is a valuable skill. Here's a step-by-step guide:
Prepare the Machine:
Ensure the excavator is on stable ground.
Engage the parking brake and turn off the engine.
Secure the Tracks:
Lift the excavator using appropriate equipment to relieve tension from the tracks.
Use track tension adjustment features to loosen the tracks.
Locate the Master Link:
Refer to the earlier steps for locating the master link.
Use the Right Tools:
Equip yourself with a suitable punch or tool designed for master link removal.
Align and Strike:
Position the tool on the master link pin.
Use a hammer or mallet to carefully strike the tool, gradually forcing the pin out.
Separate the Tracks:
Once the master link pin is removed, carefully separate the tracks, allowing access to the components that require maintenance or replacement.
Conclusion:
In conclusion, the master link in steel excavator tracks plays a pivotal role in facilitating efficient maintenance and component replacement. Understanding its importance, knowing how to locate it, and mastering the process of knocking it out are essential skills for any earthmoving equipment operator. By incorporating these practices into your maintenance routine, you not only ensure the longevity of your machine but also contribute to the overall success of your earthmoving business.
Maximizing Efficiency: A Comprehensive Guide to Excavator Tracks
Welcome to another insightful blog brought to you by Vikfin, your trusted partner in the earthmoving industry. In this edition, we will delve into the heart of excavator performance – the tracks. Understanding the nuances between steel and rubber tracks, identifying signs of wear and tear, choosing the right replacement materials, and optimizing track lifespan are all essential aspects of maintaining a robust fleet. Let's embark on this journey to ensure your excavator tracks remain in prime condition.
Steel vs. Rubber Tracks: Choosing the Right Fit
The choice between steel and rubber tracks significantly impacts the performance of your excavator. Steel tracks offer durability and stability on rough terrains, making them ideal for heavy-duty applications. On the other hand, rubber tracks provide versatility, reducing ground damage and noise while enhancing maneuverability. Assessing your specific needs and the nature of your projects will guide you in making an informed decision.
In the world of earthmoving, the choice between steel and rubber excavator tracks can significantly impact the efficiency and performance of your fleet. At Vikfin, we understand the importance of selecting the right type of track for the job at hand. We will explore the distinctive features, pros, and cons of steel and rubber tracks, guiding you towards informed decisions tailored to your specific needs.
Steel Excavator Tracks: The Robust Powerhouse
Pros:
Durability: Steel tracks are renowned for their robustness, making them ideal for heavy-duty applications. They excel in challenging terrains, providing stability and longevity.
Traction: The sturdy nature of steel tracks ensures superior traction, enabling excavators to navigate through rough surfaces, rocky landscapes, and uneven terrains with ease.
Long Lifespan: When properly maintained, steel tracks have a longer lifespan compared to rubber tracks, making them a cost-effective choice over the long run.
Cons:
Ground Impact: Steel tracks can cause more ground disturbance and damage, particularly on delicate surfaces. This makes them less suitable for projects where ground protection is a priority.
Noise Level: Steel tracks can be noisier during operation, which may be a consideration for projects in noise-sensitive environments or urban areas.
Suitable Jobs:
Steel tracks shine in heavy-duty construction and mining projects where durability and traction are paramount. They are the preferred choice for excavators working in challenging terrains that demand maximum stability and longevity.
Rubber Excavator Tracks: The Versatile Performer
Pros:
Versatility: Rubber tracks offer versatility by reducing ground damage and providing a smoother ride. They are suitable for a variety of terrains, including asphalt, concrete, and grassy areas.
Noise Reduction: Rubber tracks generate less noise during operation, making them a preferred choice for projects in noise-sensitive environments or urban settings.
Less Ground Disturbance: The lighter footprint of rubber tracks minimizes ground disturbance, making them suitable for projects where surface protection is crucial.
Cons:
Wear and Tear: Rubber tracks may experience quicker wear and tear, especially in abrasive conditions or heavy-duty applications.
Traction on Rough Terrain: While rubber tracks offer good traction on most surfaces, they may not perform as well as steel tracks in extremely rough or rocky terrains.
Suitable Jobs:
Rubber tracks are an excellent choice for construction projects on surfaces that require protection, such as finished landscapes, asphalt, or concrete. They are also well-suited for urban construction sites and projects in noise-sensitive areas.
In the dynamic world of earthmoving, the choice between steel and rubber excavator tracks boils down to the specific demands of your projects. Consider the terrain, ground protection requirements, and desired lifespan to make an informed decision that aligns with your business goals. At Vikfin, we are here to assist you in finding the perfect traction solution for your excavator fleet.
Common Causes of Wear and Tear on Steel Tracks
Understanding the common culprits behind wear and tear is crucial for effective maintenance. Steel tracks are susceptible to abrasion, especially when navigating rocky surfaces. Additionally, improper tension, misalignment, and lack of lubrication can accelerate wear. Regular inspections and proactive measures are essential to mitigate these factors.
As stalwarts in the earthmoving industry, we at Vikfin understand that the longevity and performance of your excavator tracks are vital for the success of your projects. In this blog, we'll dissect the common causes behind wear and tear on steel excavator tracks, empowering you with the knowledge to enhance the durability of your fleet.
1. Abrasive Terrain: The Silent Aggressor
One of the primary culprits behind steel track wear is the abrasive nature of the terrain. Excavators operating in rocky or abrasive environments subject their tracks to constant friction and impact. Over time, this abrasive wear can lead to the gradual thinning of the track components, compromising their structural integrity.
2. Improper Tension: Walking the Tightrope
Maintaining the correct tension in your steel tracks is crucial for optimal performance and longevity. Tracks that are either too tight or too loose can experience accelerated wear. Excessive tension can lead to increased stress on the components, while insufficient tension may result in misalignment and uneven wear. Regularly checking and adjusting the tension ensures a balanced and efficient operation.
3. Misalignment Woes: The Uneven Journey
Misalignment is a common issue that can significantly contribute to wear and tear. When tracks are not aligned correctly, certain areas bear more weight and stress than others during operation. This imbalance leads to uneven wear patterns, reducing the overall lifespan of the tracks. Regular alignment checks and adjustments are essential preventive measures.
4. Lack of Lubrication: Friction's Foe
Proper lubrication is the lifeblood of any mechanical system, and excavator tracks are no exception. Inadequate lubrication can result in increased friction between the track components, leading to accelerated wear. Regularly inspecting and lubricating the track links, rollers, and idlers is a simple yet effective way to minimize friction-related wear.
5. Harsh Operating Practices: Accelerating Aging
The way an excavator is operated can significantly impact the wear on its tracks. Harsh operating practices, such as sudden accelerations, abrupt stops, and aggressive maneuvers, can put undue stress on the tracks. Implementing smooth and controlled operating techniques not only enhances safety but also contributes to prolonged track life.
6. Environmental Factors: Nature's Influence
Environmental factors, such as exposure to extreme temperatures, moisture, and corrosive substances, can hasten the deterioration of steel tracks. Regular cleaning, protective coatings, and storing equipment in a controlled environment when not in use are effective strategies to counteract the impact of environmental elements.
Understanding the common causes of wear and tear on steel excavator tracks is the first step toward implementing proactive maintenance practices. By addressing these culprits head-on through regular inspections, proper tensioning, alignment checks, lubrication, and mindful operating practices, you can ensure that your steel tracks withstand the test of time, contributing to the overall efficiency and success of your earthmoving projects.
Signs Your Tracks Need Replacement
Identifying signs of wear early on can prevent costly repairs and downtime. Keep an eye out for uneven wear patterns, missing track links, or excessive vibration during operation. If you notice any of these indicators, it's time to consider a replacement. Timely action ensures optimal performance and minimizes the risk of further damage.
Ensuring the optimal performance of your excavator involves proactive maintenance, and one critical aspect is monitoring the condition of the tracks. At Vikfin, we understand that timely replacement is key to preventing costly downtime and maximizing efficiency. We'll explore the telltale signs that indicate it's time to change your steel excavator tracks.
1. Uneven Wear Patterns: Tread Carefully
Inspecting your tracks regularly is essential for catching early signs of wear. Uneven wear patterns across the track links or excessive wear on specific areas can indicate misalignment or other issues. If left unaddressed, uneven wear can lead to further damage and compromise the overall stability of your excavator.
2. Missing Track Links: Bridging the Gaps
The presence of missing track links is a clear indicator that your tracks are reaching the end of their lifespan. Whether due to wear, stress, or other factors, the absence of links disrupts the continuity of the track, affecting traction and stability. Prompt replacement is crucial to avoid further damage and potential safety hazards.
3. Excessive Vibration: Feeling the Rumble
If you notice an unusual increase in vibrations during operation, it could be a sign that your steel tracks are worn beyond their optimal condition. Excessive vibration indicates a lack of stability and can contribute to accelerated wear on other components. Addressing this issue promptly can prevent additional damage to your excavator.
4. Reduced Traction: Slipping Away
Traction is a fundamental aspect of excavator performance. If you observe a noticeable reduction in traction, especially on familiar terrains, it may be an indication that your steel tracks are worn. This can affect the efficiency of your operations and compromise safety. Replace worn tracks to restore optimal traction and ensure the smooth operation of your excavator.
5. Track Joint Movement: Excessive Play
Excessive movement or play at the track joints is a clear sign that your tracks have worn beyond their serviceable limit. This can lead to misalignment, increased stress on components, and a decline in overall performance. Regularly check for any play in the track joints and take corrective action when necessary.
6. Visible Damage: Inspect and Detect
Physical damage, such as cracks, dents, or bent components, is an unmistakable sign that your steel tracks require replacement. Even minor damage can compromise the structural integrity of the tracks and escalate into more significant issues if not addressed promptly.
7. Reduced Ground Clearance: A Low Point
If your excavator's ground clearance is noticeably reduced, it may be a result of worn tracks. As the tracks wear down, the overall height of the machine decreases. Monitoring ground clearance regularly can help you identify gradual wear and plan for timely track replacement.
Being attuned to these signs can save you from unexpected downtime, costly repairs, and potential safety hazards. Regular inspections, coupled with proactive maintenance practices, will ensure that your steel excavator tracks remain in optimal condition, contributing to the longevity and efficiency of your earthmoving fleet. Trust Vikfin for all your earthmoving needs, and stay tuned for more insights to empower your business.
The Steel Composition: Unveiling the Mystery
The type of steel used in manufacturing tracks plays a pivotal role in their longevity. At Vikfin, we prioritize high-quality materials that withstand the rigors of demanding environments. Our tracks are crafted from hardened steel alloys, ensuring durability and resistance to impact and abrasion.
In the construction of excavator tracks, high-quality and durable steel alloys are commonly employed to withstand the demanding conditions and heavy loads encountered in earthmoving operations. The specific type of steel used can vary among manufacturers, but generally, excavator tracks are crafted from hardened or alloyed steel to enhance their strength and resistance to wear and tear.
Hardened steel typically contains carbon as the primary alloying element, and the hardening process involves heat treatment to increase the steel's hardness and durability. Additionally, manganese and other alloying elements may be included to further enhance the steel's toughness and wear resistance.
The exact composition and grade of steel can vary based on factors such as the manufacturer's specifications, the type of excavator, and the intended use of the tracks. It's common for manufacturers to use high-strength steel alloys to ensure the tracks can withstand the challenging conditions of construction sites, including abrasion from rocky terrains and heavy loads.
For precise information about the type of steel used in the excavator tracks you are interested in, it's recommended to consult with the equipment manufacturer or supplier. They can provide detailed specifications regarding the steel composition, heat treatment processes, and other relevant details specific to their products.
Changing Excavator Tracks: A Step-by-Step Guide
When the time comes for replacement, having a clear understanding of the process is essential. Begin by lifting the excavator using appropriate equipment and securing it safely. Remove the nuts and bolts holding the old tracks, carefully detach the links, and install the new tracks. Proper tensioning and alignment are critical for optimal performance.
Changing steel excavator tracks is a detailed process that requires careful attention to safety and proper equipment. Here is a step-by-step guide to changing steel excavator tracks:
1. Gather Necessary Equipment:
Heavy-duty lifting equipment (such as a crane or hydraulic jack)
Appropriate safety gear (gloves, safety glasses, etc.)
Wrenches, sockets, and other tools for removing nuts and bolts
Track tension gauge
2. Ensure Safety:
Park the excavator on a flat and stable surface.
Engage the parking brake and turn off the engine.
Use safety blocks to prevent the excavator from rolling during the process.
3. Lift the Excavator:
Use a crane or hydraulic jack to lift the excavator off the ground.
Ensure that the lifting points are secure and can support the weight of the machine.
4. Remove the Old Tracks:
Locate the nuts and bolts securing the track links.
Use appropriate tools to remove the nuts and bolts, allowing you to disassemble the track links.
Carefully detach the old tracks from the sprocket and idler.
5. Check Components:
Inspect the sprockets, idlers, and other track components for signs of wear or damage.
Replace any worn or damaged components as necessary.
6. Install the New Tracks:
Position the new tracks around the sprocket and idler.
Connect the track links, ensuring proper alignment.
Insert the bolts and nuts and tighten them securely.
7. Adjust Track Tension:
Use a track tension gauge to ensure the proper tension of the tracks.
Adjust the tension according to the manufacturer's specifications.
Proper tension prevents premature wear and enhances performance.
8. Lower the Excavator:
Carefully lower the excavator back to the ground using the crane or hydraulic jack.
9. Final Adjustments:
Double-check the track tension and alignment.
Start the excavator and operate it in a controlled manner to ensure that the tracks are functioning correctly.
Make any additional adjustments if necessary.
10. Post-Installation Inspection:
Conduct a thorough inspection of the entire track system.
Look for any signs of abnormal wear, misalignment, or other issues.
Address any issues immediately to prevent further damage.
11. Dispose of Old Tracks:
Properly dispose of the old tracks according to local regulations.
It's crucial to follow the manufacturer's guidelines and recommendations for your specific excavator model during the track replacement process. If you are not familiar with the process, it is advisable to consult with a qualified technician or the equipment manufacturer for guidance. Additionally, always prioritize safety during every step of the process.
Extending Track Lifespan: Best Practices
Preventive measures are the key to maximizing the lifespan of your excavator tracks. Regularly inspect and clean tracks to remove debris that can accelerate wear. Maintain proper tension, ensure alignment, and lubricate components as recommended. Additionally, consider the terrain and adjust your operating practices accordingly.
Extending the lifespan of steel excavator tracks is essential for maximizing the efficiency and longevity of your earthmoving equipment. Implementing proper maintenance practices and adopting a proactive approach can significantly contribute to prolonging the lifespan of your steel tracks. Here are some key strategies:
Regular Inspections:
Conduct routine visual inspections of the tracks to identify signs of wear, damage, or misalignment.
Check for loose or missing bolts, damaged track links, and abnormal wear patterns.
Inspect the sprockets, idlers, and rollers for wear and tear.
Proper Track Tension:
Maintain the correct tension in the tracks to prevent premature wear.
Refer to the manufacturer's specifications for the recommended track tension.
Regularly check and adjust the tension as needed.
Lubrication:
Ensure proper lubrication of all moving components, including track links, rollers, and idlers.
Use the recommended lubricants and follow the manufacturer's guidelines for lubrication intervals.
Regular lubrication reduces friction and minimizes wear on the steel tracks.
Terrain Awareness:
Be mindful of the terrain your excavator operates on.
Avoid unnecessary stress on the tracks by selecting appropriate paths and navigating carefully through challenging terrains.
Minimize operation on abrasive surfaces when possible.
Operational Best Practices:
Train operators on smooth and controlled operating practices.
Avoid sudden accelerations, abrupt stops, and aggressive maneuvers that can increase stress on the tracks.
Encourage operators to follow recommended operating guidelines provided by the equipment manufacturer.
Environmental Protection:
Protect steel tracks from exposure to corrosive materials and harsh environmental conditions.
Clean the tracks regularly to remove debris, mud, and other materials that can contribute to wear.
Consider using protective coatings to enhance resistance to corrosion.
Prompt Repairs:
Address any issues or signs of wear immediately.
Replace damaged or worn components promptly to prevent further damage to the tracks.
Regularly check and replace missing or loose nuts and bolts.
Track Pads and Shoes:
Consider using track pads or shoes designed for specific applications to reduce wear on the tracks.
Choose track pads made from materials that offer durability and resistance to abrasion.
Training and Awareness:
Train your maintenance team and operators on proper maintenance procedures.
Foster a culture of awareness regarding the importance of maintaining equipment for optimal performance and longevity.
Documented Maintenance Records:
Keep detailed records of maintenance activities, inspections, and repairs.
Use these records to track the condition of the tracks over time and schedule preventive maintenance accordingly.
By incorporating these practices into your maintenance routine, you can enhance the lifespan of your steel excavator tracks, reduce operational costs, and ensure the continued efficiency of your earthmoving equipment. Regular and proactive maintenance is key to preserving the integrity of your equipment and minimizing downtime.
In conclusion, excavator tracks are the backbone of efficient earthmoving operations. By understanding the differences between steel and rubber tracks, recognizing signs of wear, choosing high-quality materials, and following proper maintenance procedures, you can ensure your fleet operates at peak performance. Trust Vikfin for all your earthmoving needs, and stay tuned for more industry insights that empower your business.
#heavyequipment#construction#excavator#heavymachinery#constructionequipment#heavyequipmentlife#caterpillar#earthmoving#mining#excavation#komatsu#equipment#heavyequipmentnation#cat#digger#excavators#demolition#heavyequipmentoperator#machinery#constructionlife#engineering#truck#concrete#bulldozer#earthmovers#constructionmachinery#civilengineering
Comments