How to Reduce Downtime in Construction & Mining with Fast Spare Part Sourcing
- RALPH COPE
- Feb 6
- 4 min read
Updated: Feb 7
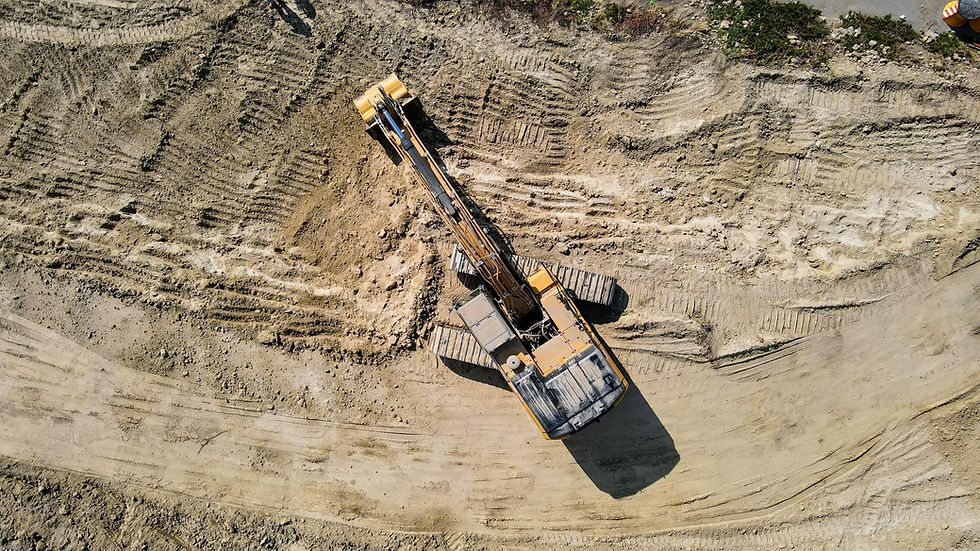
The Cost of Delays: Why Every Minute Counts
In the fast-paced world of construction and mining, every hour of downtime means lost revenue, project delays, and potential contractual penalties. Machinery failures are inevitable, but how quickly you source and replace a faulty part can make the difference between a minor inconvenience and a major financial disaster.
Imagine this: A critical excavator breaks down on a mining site, and the required replacement part isn’t immediately available. The machine sits idle for three days, causing a ripple effect across the entire project. Workers remain on-site but unproductive, deadlines are pushed back, and additional costs pile up. The financial impact? Catastrophic.
This is why efficient spare part sourcing is the backbone of operational success in industries that depend on heavy earthmoving equipment. At Vikfin, we understand that time is money, which is why we have a large stock of OEM parts ready for immediate dispatch.
The Real Cost of Downtime in Rands (ZAR)
To grasp the financial impact of downtime, let’s break it down into cold, hard numbers:
Equipment Type | Average Downtime Cost per Hour | Downtime Cost per Day (8 hrs) |
Excavator (20-ton) | R3,000 | R24,000 |
Articulated Dump Truck | R4,500 | R36,000 |
Bulldozer | R6,000 | R48,000 |
Wheel Loader | R5,500 | R44,000 |
Mining Drill Rig | R10,000 | R80,000 |
For a large construction or mining company running multiple machines, a single day of unplanned downtime can cost upwards of R500,000 when you factor in labor costs, project delays, and contractual penalties.
Why Spare Part Delays Happen – And How to Avoid Them
1. Lack of Local Stock: Many companies rely on OEMs (Original Equipment Manufacturers) or authorized dealers for parts, but these sources often have long lead times, particularly for specialized components.
Solution: Vikfin stocks a massive range of used OEM parts that are fully refurbished, tested, and ready for immediate dispatch, cutting out unnecessary wait times.
2. Import Delays & High Costs:Ordering parts from overseas means you’re at the mercy of shipping schedules, customs delays, and fluctuating exchange rates. A component that costs R50,000 abroad can easily end up costing R75,000 after shipping, duties, and markups.
Solution: Vikfin sources parts locally to eliminate these issues, ensuring same-day or next-day delivery across South Africa.
3. Incorrect Parts Ordered: A significant percentage of downtime is caused by ordering the wrong part. When a machine is down, pressure mounts to find a replacement quickly, and rushed decisions lead to costly mistakes.
Solution: Vikfin’s team of experienced specialists helps businesses identify and source the exact part they need, ensuring perfect compatibility with their machines.
How Vikfin Minimizes Downtime
At Vikfin, we have fine-tuned our spare parts supply chain to make sure businesses in construction and mining don’t suffer from unnecessary delays. Here’s how:
1. Massive Inventory of OEM Parts
We stock high-quality used and refurbished OEM parts, covering all major brands, including:
Caterpillar
Komatsu
Volvo
Hitachi
Doosan
JCB
Sumitomo
Hyundai
Bell
Liebherr
Whether it’s an engine, final drive, hydraulic pump, slew motor, track adjuster, or transmission, we have thousands of parts available for immediate shipping.
2. Competitive Pricing That Beats the Market
We don’t just focus on availability – we focus on value. Buying a brand-new part from an OEM can cost 2-3 times more than a high-quality refurbished OEM part from Vikfin.
For example:
Part | OEM Price (New) | Vikfin Price (Refurbished) | Savings (%) |
Final Drive (Komatsu PC200) | R180,000 | R95,000 | 47% |
Hydraulic Pump (Caterpillar 320D) | R240,000 | R125,000 | 48% |
Slew Motor (Volvo EC210) | R150,000 | R85,000 | 43% |
3. Fast Nationwide Delivery
We partner with the best logistics providers to offer same-day and next-day delivery across South Africa. This ensures that businesses in Johannesburg, Cape Town, Durban, or remote mining areas can get their machines back to work without long delays.
4. Expert Guidance – The Right Part, First Time
Our team of specialists knows the industry inside out. Instead of blindly searching for parts, you can consult with experts who will help you find the exact component you need without wasting time or money.
5. We Buy & Strip Machines for Spares
To ensure a steady stock of hard-to-find components, we actively purchase high-hour and older excavators for stripping. This allows us to carry rare parts no longer manufactured or difficult to import.
Why Businesses Trust Vikfin
✅ We save companies millions of rands annually by providing fast, cost-effective solutions. ✅ We guarantee the lowest prices on OEM spare parts – if you find a better deal, we’ll beat it. ✅ We eliminate the frustration of long waits, incorrect orders, and overpriced parts. ✅ We offer a customer-centric approach, ensuring businesses get exactly what they need.
The Bottom Line: Reduce Downtime, Increase Profits
The faster you replace a broken part, the faster you get your machine back to work. Every hour saved equals thousands of rands retained. By partnering with Vikfin, construction and mining businesses can stay ahead of breakdowns, cut costs, and maintain productivity.
Don’t let your machines sit idle and cost you money. Get in touch with Vikfin today and experience the fastest spare part sourcing in South Africa.
📞 Call us now: 071 351 9750📧 Email us: admin@vikfin.co.za🌍 Visit us: www.vikfin.co.za
#ExcavatorParts #MiningEquipment #ConstructionLife #HeavyMachinery #Earthmoving #Komatsu #Caterpillar #VolvoExcavator #HydraulicParts #OEMParts #SpareParts #PlantHire #EquipmentRepair #FinalDrive #HydraulicPump #SlewMotor #KomatsuPC200 #MachineDowntime #MiningSouthAfrica #VikfinParts
Comments