Excavator Hammers: The Ultimate Guide to Versatility, Durability, and Maintenance
- RALPH COPE
- Sep 9, 2024
- 8 min read
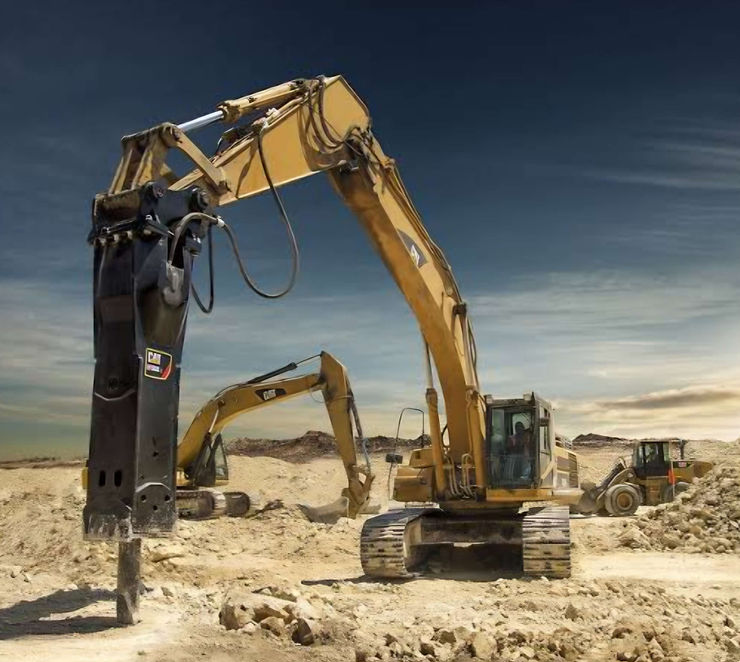
When it comes to construction and demolition, an excavator with a hammer attachment is like a multi-functional tool capable of handling the toughest tasks. The hammer, also referred to as a hydraulic breaker, is one of the most efficient and powerful attachments an excavator can use. Its ability to break through tough materials like concrete, rock, and asphalt has made it a must-have tool on many job sites. In this blog, we will take a deep dive into everything you need to know about excavator hammers, from their construction to their common uses, how they are attached, maintenance tips to extend their lifespan, signs of failure, and finally, the critical decision of whether to repair or replace a failing hammer.
What Is an Excavator Hammer?
An excavator hammer, also known as a hydraulic breaker, is a heavy-duty attachment designed to break through hard surfaces. It operates by using a piston that moves up and down inside a cylinder. This movement transfers the energy through the attachment's tool—a chisel or moil point—which then penetrates or breaks the material beneath it.
While often seen on construction and demolition sites, hammers are versatile tools that can be used across a range of industries, including mining, quarrying, and even specialized underwater applications.
How is an Excavator Hammer Constructed?
The construction of an excavator hammer is a fascinating process of engineering precision. The main components of a hammer attachment include:
Housing: The outer shell that contains and protects the internal components of the hammer.
Cylinder: Located inside the housing, this is where the piston moves to generate the force needed for the hammer to break materials.
Piston: The moving part inside the cylinder that creates the percussive force. It transfers the energy from the hydraulic pressure into mechanical energy to drive the chisel or point.
Tool (Chisel or Moil Point): The business end of the hammer, which makes contact with the material. The type of tool used will depend on the task at hand. Moil points are generally used for breaking through hard materials like rock, while chisels are more appropriate for concrete or asphalt.
Accumulator: A chamber that stores hydraulic energy and helps regulate pressure inside the hammer. This component improves the hammer's efficiency by delivering additional power during the piston’s striking motion.
Hydraulic Valves: These control the flow of hydraulic fluid into the hammer and regulate the pressure, which drives the piston up and down.
Bushings and Seals: These protect the internal components and prevent the hydraulic fluid from leaking.
Types of Jobs Excavator Hammers Are Used For
Excavator hammers can be found on a wide variety of job sites due to their versatility and power. Some of the common tasks they are used for include:
Demolition: Hammers are perfect for demolishing concrete structures such as old buildings, bridges, and pavement.
Rock Breaking: In quarries, mines, and road construction, hammers are used to break large rocks and boulders into manageable sizes.
Trenching and Foundation Work: For hard soils or rocks, hammers can assist in digging trenches or creating foundations for new structures.
Underwater Applications: In marine construction, underwater hammers can be used for rock breaking, pile driving, and demolition in submerged environments.
Asphalt Removal: Hammers are often employed to break apart asphalt for road maintenance and repairs.
Utility Work: In utility and pipeline projects, hammers are used to excavate hard ground or demolish existing infrastructure.
How is a Hammer Attached to an Excavator?
Attaching a hammer to an excavator is a relatively straightforward process, but it must be done correctly to ensure safety and proper operation. Most excavators are equipped with quick coupler systems, which make the attachment process simpler and faster. Here are the steps to attach a hammer to an excavator:
Safety First: Before starting, ensure the excavator is turned off, and the hydraulic pressure is released to avoid accidents.
Remove the Existing Attachment: If another attachment is already connected to the excavator, remove it using the quick coupler or manually detach it.
Inspect the Hammer: Before installation, check the hammer for any signs of damage, leaks, or wear. Also, ensure that the hammer’s hydraulic hoses and couplings are clean and free from debris.
Connect the Hammer to the Quick Coupler: Position the hammer attachment so that the quick coupler can easily lock onto it. Once in position, lock the coupler in place.
Connect the Hydraulic Lines: Attach the hydraulic hoses from the excavator to the hammer. Ensure that the connections are secure and the hoses are free from kinks or bends.
Test the Attachment: After attaching the hammer, turn on the excavator and slowly activate the hydraulic system to test the hammer’s functionality. Make sure it is operating correctly and that there are no hydraulic leaks.
Extending the Life of Your Excavator Hammer
A hydraulic hammer is a significant investment, and maintaining it properly can extend its life and maximize its efficiency. Here are several tips to ensure your hammer lasts as long as possible:
Regular Lubrication: The moving parts of a hammer need regular lubrication to prevent wear and tear. A specific type of grease, designed for high-pressure applications, should be used. Lubricate the tool after every few hours of use, depending on the working conditions.
Proper Alignment: When using the hammer, make sure it is properly aligned with the material being broken. Misalignment can lead to premature wear on the tool and the bushings.
Avoid Blank Firing: Blank firing occurs when the hammer is activated without making contact with the material. This can cause unnecessary wear on internal components, so always make sure the tool is pressed against the material before firing.
Inspect Regularly: Regularly inspect your hammer for signs of damage, such as cracks in the housing, leaks, or worn seals. Early detection of these issues can prevent more significant, costly repairs down the line.
Monitor Hydraulic Pressure: Ensure that the hydraulic pressure is set correctly for the hammer. Too much pressure can damage the internal components, while too little pressure will make the hammer less effective.
Replace Worn Parts: The bushings, seals, and tool points are all subject to wear and should be replaced when necessary to keep the hammer operating efficiently.
Most Common Ways in Which an Excavator Hammer is Damaged
Despite their durability, hydraulic hammers can still be damaged through improper use or neglect. Here are some of the most common ways in which they are damaged:
Overuse: Continuously running a hammer without giving it time to cool down can overheat the hydraulic system and damage internal components.
Misuse: Using the hammer on materials that it is not designed to break, such as metal or certain types of reinforced concrete, can damage the tool point and piston.
Improper Storage: Storing the hammer in a damp or dirty environment can lead to corrosion and contamination of the hydraulic fluid.
Hydraulic Leaks: Damage to the seals or hoses can cause hydraulic fluid to leak, which reduces the hammer’s effectiveness and can cause internal damage if not addressed promptly.
Blank Firing: As mentioned earlier, blank firing can cause serious damage to the internal components of the hammer.
How to Know Your Hammer May Be Failing
It's crucial to be aware of the signs that your excavator hammer may be nearing the end of its life. Catching these signs early can help you avoid catastrophic failures that could lead to costly downtime. Here are some of the warning signs to look out for:
Reduced Impact Force: If the hammer is not hitting as hard as it used to, this could indicate a loss of hydraulic pressure, worn bushings, or internal damage to the piston.
Hydraulic Leaks: Leaking fluid is a clear sign that seals or hoses need to be replaced. Left unaddressed, leaks can lead to significant internal damage.
Unusual Noises: Any strange sounds, such as grinding or banging, during operation may indicate that parts inside the hammer are wearing out or have been damaged.
Tool Point Wear: Excessive wear on the tool point can reduce the hammer's effectiveness. If the tool point is mushroomed or deformed, it is time to replace it.
Cracks or Damage to the Housing: Cracks in the hammer’s housing are a serious issue that can lead to complete failure. If you notice any structural damage, stop using the hammer and have it inspected immediately.
Repair vs. Replace: How to Decide
When your excavator hammer starts to show signs of failure, the decision of whether to repair or replace it can be difficult. Several factors should be taken into account:
Age of the Hammer: If the hammer is relatively new and has not seen extensive use, it may be worth repairing. However, if the hammer is old and has been heavily used, replacing it may be the better long-term investment.
Cost of Repairs: If the cost of repairs is close to or exceeds the cost of a new hammer, replacement is the obvious choice. However, minor repairs, such as replacing seals or tool points, can be done relatively inexpensively and can extend the life of the hammer.
Frequency of Breakdowns: If the hammer has been requiring frequent repairs, it may be a sign that it is nearing the end of its useful life. In this case, replacement might be the more cost-effective option in the long run. Continuously investing in repairs for an old or heavily worn hammer can add up and still leave you with an underperforming tool.
Availability of Parts: If replacement parts for your hammer are difficult to find or expensive, this could also push you toward replacing the hammer altogether. On the other hand, if parts are readily available and affordable, a repair might be the better choice.
Impact on Productivity: If your hammer is essential to the productivity of your business, consider how much downtime you can afford. In some cases, it may be faster and more cost-effective to replace the hammer immediately rather than waiting for repairs to be completed, especially if those repairs require hard-to-find parts.
Resale Value: Depending on the condition of the hammer and its remaining life, it may still have some resale value. Selling a failing hammer that still has some life left in it can help offset the cost of a new one.
Conclusion
An excavator hammer is a vital tool for many industries, from construction and demolition to mining and quarrying. However, like any piece of heavy equipment, it requires proper care and maintenance to maximize its lifespan.
Understanding the hammer’s construction, how it works, and how it can be attached to an excavator is essential for optimal performance. Regular inspections, lubrication, and hydraulic monitoring can help extend the hammer’s life, while knowing the common signs of failure ensures you can address problems early before they result in expensive downtime.
Finally, when your hammer does start to fail, you’ll need to make the crucial decision of whether to repair or replace it. Taking into account the hammer's age, repair costs, and the impact on your productivity will guide you toward the right choice. Whether you choose to repair or replace, having a well-maintained, high-performing hammer can make a significant difference in the efficiency and profitability of your operations.
If you're in the market for high-quality used excavator hammers or need expert advice on maintaining your current one, Vikfin offers a range of OEM parts and attachments to keep your equipment running smoothly. Investing in reliable parts from a trusted provider can help ensure your hammer attachment continues to deliver powerful performance, no matter the job.
留言