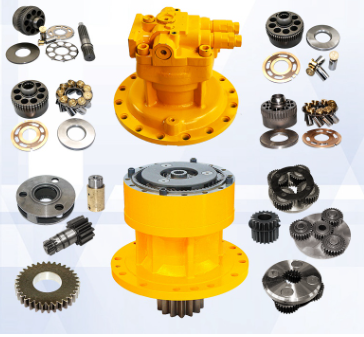
Excavators play a vital role in construction and earthmoving projects, and their efficient functioning relies on the proper maintenance and servicing of various components. One crucial component is the slew motor, responsible for controlling the rotational movement of the excavator. In this blog post, we will provide a step-by-step guide on how to service the slew motor on an excavator, helping operators and technicians ensure optimal performance and extend the lifespan of this essential equipment.
Understanding the Slew Motor
Before diving into the servicing process, it is crucial to understand the basic workings of the slew motor. The slew motor is typically located on the excavator's upper structure, and it drives the rotation of the excavator's platform or house. This allows the operator to position the machine accurately and perform tasks efficiently.
Preparing for Servicing
Safety first: Always prioritize safety. Park the excavator on level ground, engage the parking brake, and shut off the engine before starting any maintenance work.
Gather the necessary tools: Prepare a toolkit that includes items such as wrenches, sockets, lubricants, cleaning materials, and a torque wrench. Consult the equipment's manual to ensure you have the correct tools for the job.
Inspect the motor: Visually examine the slew motor for any signs of leaks, damage, or excessive wear. If you notice anything unusual, consult a qualified technician before proceeding.
Servicing the Slew Motor
Cleaning the motor: Begin by cleaning the exterior of the motor using a mild detergent and a cloth or brush. Remove any dirt, debris, or accumulated grease. Avoid using excessive water, especially near electrical connections or components.
Inspecting electrical connections: Inspect the slew motor's electrical connections for corrosion or loose connections. If necessary, tighten or replace any damaged connections. Ensure all electrical connections are secure.
Lubrication: Consult the equipment manual to determine the type and amount of lubricant required. Apply the appropriate lubricant to the motor's rotating parts, such as bearings and gears. Use a grease gun or appropriate applicator for precision.
Checking hydraulic fluid: Examine the hydraulic fluid level and quality in the excavator. If the fluid is low or contaminated, refer to the equipment manual for proper fluid specifications and replacement instructions.
Adjusting the slew motor: Over time, the slew motor may require adjustments to maintain optimal performance. Consult the manual to identify the adjustment points and follow the recommended procedures.
Inspecting wear components: Carefully examine the slew motor's wear components, such as seals, gaskets, and gears. Look for signs of damage, wear, or leaks. Replace any worn or damaged components as necessary.
Torque checks: Using a torque wrench, check the torque of the mounting bolts and fasteners on the slew motor. Ensure they are tightened to the manufacturer's specifications.
Testing and calibration: Once the servicing is complete, start the excavator and test the slew motor's operation. Ensure smooth rotation and functionality in both directions. If any issues arise, consult a professional technician for further evaluation.
Regular Maintenance Tips
To keep your excavator's slew motor in excellent condition, consider the following maintenance tips:
Keep the motor and surrounding area clean to prevent debris accumulation.
Follow the manufacturer's recommended maintenance schedule.
Regularly inspect and replace hydraulic fluid and filters as necessary.
Monitor the motor's performance for any signs of abnormalities or decreased efficiency.
Train operators to use the excavator correctly to minimize unnecessary strain on the motor.
Servicing the slew motor on an excavator is essential to maintain its performance and extend its lifespan. By following the steps outlined in this guide and adopting regular maintenance practices, operators and technicians can ensure the reliable and efficient operation of this critical component in their excavator fleet.
Note: The Function of the Brakes in a Slew Motor
Ensuring Safe and Controlled Rotation
The slew motor is responsible for the rotational movement of an excavator. It allows the machine to swivel and position the boom and bucket in different directions. The brakes within the slew motor serve the crucial purpose of controlling and halting this rotational movement when necessary.
During operation, an excavator may need to stop abruptly or maintain a specific position while lifting or digging. In such instances, the brakes engage to prevent any unintended rotation, ensuring the excavator remains stable and secure. This capability is particularly vital when working on uneven or inclined surfaces, reducing the risk of accidents and enhancing overall safety.
Managing Loads and Preventing Overrun
Excavators are designed to handle heavy loads, and the brakes in the slew motor play a crucial role in managing these loads effectively. When lifting or carrying materials, the excavator relies on the brakes to prevent the slew motor from rotating freely due to the weight. By controlling the rotational speed and preventing overrun, the brakes help maintain stability and prevent the machine from tipping over.
Moreover, the brakes assist in counteracting external forces that may affect the excavator's balance. They provide resistance against momentum and enable precise control, allowing operators to maneuver the machine smoothly and safely, even with substantial loads.
Enhancing Operator Control and Precision
Excavator operators require precise control over the machine's movements to ensure accurate positioning and digging. The brakes within the slew motor contribute significantly to achieving this level of control and precision. By applying appropriate friction and resistance, the brakes enable operators to manipulate the excavator's rotation speed and bring it to a halt precisely where desired.
Additionally, the brakes facilitate fine adjustments during intricate tasks such as trenching or working in confined spaces. Operators can rely on the braking system to make subtle changes to the excavator's position, aligning it with precision to complete tasks with accuracy and efficiency.
Braking Technologies and Innovations
Over the years, braking technologies within the slew motor of excavators have evolved, bringing improvements in safety, reliability, and performance. Modern excavators employ various brake types, including hydraulic, mechanical, and electronic systems, each designed to meet specific operational requirements.
Hydraulic braking systems utilize fluid pressure to engage and disengage the brakes, providing smooth and responsive control. Mechanical braking systems employ friction discs and pads to create resistance, ensuring rapid and reliable braking performance. Electronic braking systems offer advanced control features and can be integrated with the excavator's overall control system, allowing for enhanced automation and safety.
The function of brakes within the slew motor of an excavator is crucial for maintaining safety, control, and performance. These brakes enable operators to halt rotation, manage loads effectively, and maneuver the machine with precision. With advancements in braking technologies, excavators are now equipped with highly reliable and responsive braking systems that contribute to the overall efficiency and safety of the machine.
Indications you may need to replace the slew motor of your excavator
Determining whether you need to replace the slew motor of your excavator typically involves a combination of visual inspection, listening for abnormal sounds, and monitoring the performance of the motor. Here are some signs that may indicate the need for replacement:
Reduced Power or Speed: If you notice a decrease in the excavator's rotation speed or a loss of power during operation, it could indicate a problem with the slew motor. The motor may struggle to rotate the excavator or fail to reach the expected speed.
Unusual Noises: Pay attention to any unusual or excessive noises coming from the slew motor. Grinding, whining, clunking, or squealing sounds can indicate internal damage or worn-out components, suggesting the need for replacement.
Fluid Leaks: Inspect the motor and surrounding area for any signs of hydraulic fluid leaks. Leaks can indicate damaged seals, gaskets, or other components, which may affect the motor's performance. Excessive fluid loss can lead to inadequate lubrication and overheating.
Overheating: If the slew motor becomes excessively hot during operation, it could be a sign of internal problems or inadequate lubrication. Overheating can lead to premature wear and reduced motor efficiency.
Irregular Movements: Observe the excavator's movements while operating. If you notice jerky or inconsistent rotation, sudden stops, or difficulty maintaining a specific position, it could indicate issues with the slew motor.
Increased Vibrations: Excessive vibrations during operation may suggest problems with the motor's internal components or mounting. Excessive wear or misalignment can cause vibrations, affecting the excavator's performance.
Diagnostic Testing: Some modern excavators have built-in diagnostic systems that can provide error codes or feedback on motor performance. Consult the excavator's manual or contact the manufacturer for information on how to perform diagnostic tests or retrieve error codes.
If you observe any of these signs, it is advisable to consult a qualified technician or a dealership specializing in excavator repairs. They can inspect the motor thoroughly, diagnose the problem, and recommend whether repair or replacement is necessary.
#heavyequipment#construction#excavator#heavymachinery#constructionequipment#heavyequipmentlife#caterpillar#earthmoving#mining#excavation#komatsu#equipment#heavyequipmentnation#cat#digger#excavators#demolition#heavyequipmentoperator#machinery#constructionlife#engineering#truck#concrete#bulldozer#earthmovers#constructionmachinery#civilengineering
Comments